Vehicle underbodies made from natural fibers and recycled plastics
In collaboration with industrial partners, researchers at the Fraunhofer WKI have developed a vehicle underbody made from natural fibers and recycled plastics for automotive construction. The component fulfills the stringent technical requirements in the underbody area and could replace conventional lightweight vehicle underbodies in the future. With this development, the climate and environmental balance is optimized throughout the entire product life cycle. The focus at the Fraunhofer WKI was directed at the development of the materials for injection molding as well as the hydrophobization of flax and hemp fibers for natural-fiber-reinforced mixed-fiber non-wovens.
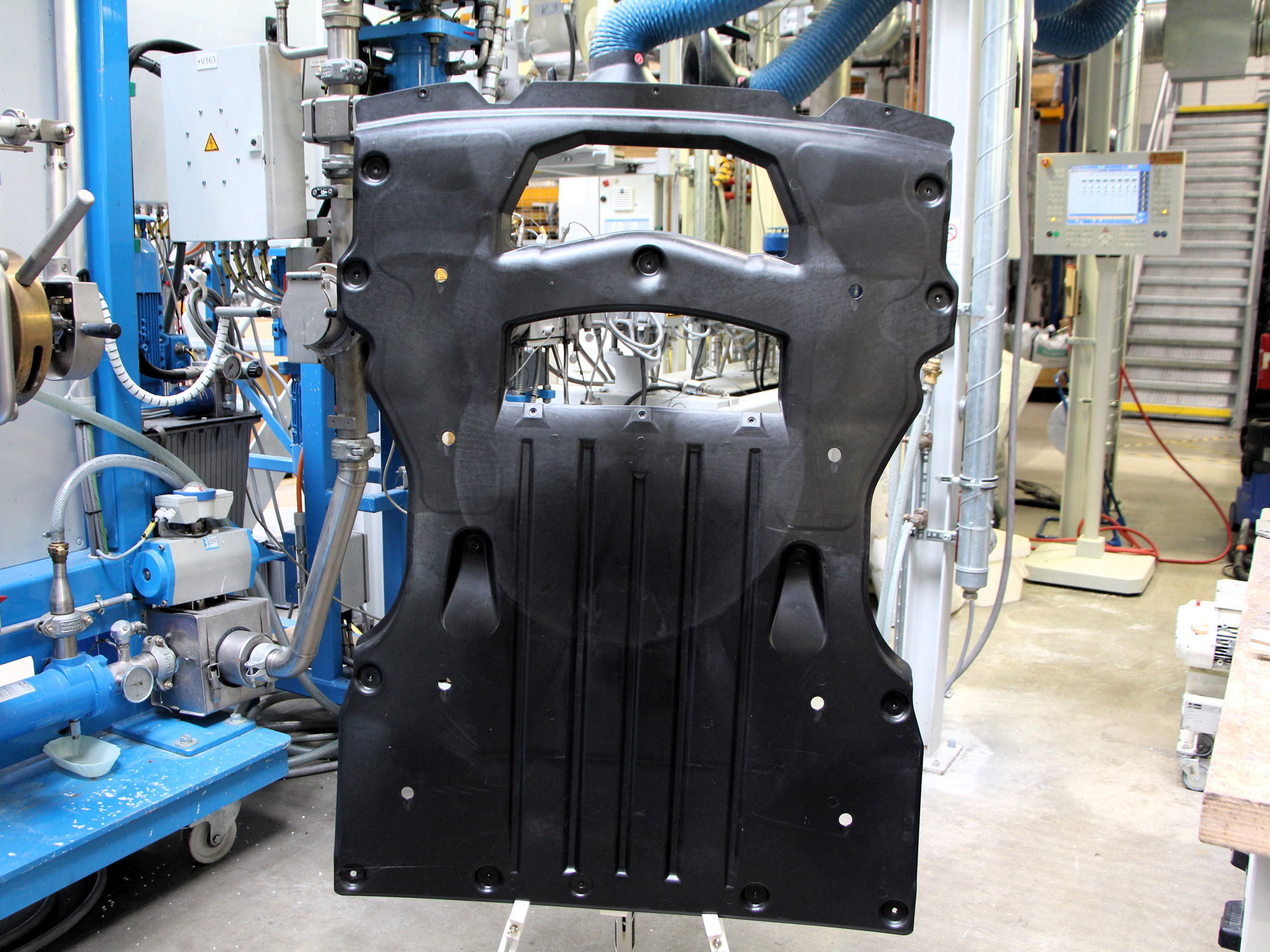
The project partners Fraunhofer WKI, Thuringian Institute for Textile and Plastics Research (TITK), Röchling Automotive SE & Co. KG, BBP Kunststoffwerk Marbach Baier GmbH and Audi AG have succeeded in developing a sustainable overall concept for vehicle underbodies. The researchers have thereby taken a challenging component group with a high plastic content and made it accessible for the utilization of natural materials. Until now, natural-fiber-reinforced plastics have predominantly been used in cars for trim parts without significant mechanical functions. Structural components such as vehicle underbodies are, however, exposed to enormous loads and place high demands on the bending and crash behavior of the material. In modern lightweight vehicle concepts, high-performance materials made from glass-fiber-reinforced plastics are therefore utilized.
The project team was able to replace the glass fibers with natural materials such as flax, hemp and cellulose fibers and to produce underbody components with a natural-fiber content of up to 45%. In the area of polymers, virgin polypropylene was completely dispensed with and solely recyclates were utilized. All the challenges associated with this material changeover – both the lower initial mechanical properties of the materials and the temporally restricted processing windows – were solved by means of skillful compound combinations.
At the Fraunhofer WKI, materials for injection molding were developed. “Natural-fiber injection-molded compounds have so far been known primarily for their increased strength and stiffness compared to non-reinforced polymers. In the development of the vehicle underbody, we have furthermore succeeded in fulfilling the stringent requirements for low-temperature impact strength through an innovative combination of selected post-consumer recyclates (PCR) as a matrix and natural fibers of varying degrees of purity - without forfeiting the required stiffness and strength,” explained Moritz Micke-Camuz, Project Manager at the Fraunhofer WKI.
Within the framework of the development, fiber-composite components made from natural-fiber-reinforced mixed-fiber non-wovens (lightweight-reinforced thermoplastic, LWRT) were realized for the first time at the TITK and at Röchling. The developed product not only fulfills the mechanical requirements: It also withstands in particular the challenges posed by the humid environment in which it is used. For the hydrophobization of flax and hemp fibers for LWRT components, a continuous furfurylation process was developed at the Fraunhofer WKI. Through furfurylation, moisture absorption can be reduced by up to 35 percent without impairment of the bending strength of the subsequent components. The furfurylated fiber material can also be easily processed on a non-woven production line.
The prototype components produced were subsequently extensively tested both at component level and in road tests. Amongst others, the vehicles from the VW Group’s new “Premium Platform Electric” (PPE) were used for this purpose. Long-term experience has already been gathered within the framework of the series testing. The gratifying result of these tests: The newly developed biocomposites fulfill all standard requirements for underbody components and have proven to be suitable for series production. Neither the use of natural fibers nor of (post-consumer) recyclates leads to a significant impairment of the properties.
One major advantage of the innovation is the significantly improved carbon footprint: Compared to series production, 10.5 kilograms of virgin material (PP/glass fiber) can be replaced by 4.2 kilograms of natural fibers and 6.3 kilograms of post-consumer recyclate. As a result, CO2 emissions during production, use and product life have been reduced by up to 40 percent.
Within the scope of the development project, an innovative, holistic overall concept for vehicle underbodies, including recycling with cascading re-use of the components, was developed. From a technical point of view, vehicle underbodies can be manufactured entirely from the new, high-performance lightweight bio construction material in the future.
Last modified: