Hannover Messe: Fraunhofer WKI presents innovative materials and components made from renewable raw materials
From raw materials to recycling - at the Hannover Messe from the 22nd to the 26th of April 2024, the Fraunhofer WKI will be presenting new application possibilities for renewable raw materials at the Fraunhofer joint stand (Hall 2, Stand B24). The examples range from a wooden crash barrier for road traffic through to sustainable concrete construction materials made from residual materials. They demonstrate the potential of renewable raw materials for the circular economy.
The products developed at the Fraunhofer WKI demonstrate that there are numerous possibilities for replacing finite resources such as concrete or steel – in whole or in part – with renewable raw materials. Whether for the construction industry or the transport sector, the solutions provide a contribution towards improving resource efficiency and the ecological balance in climate-intensive areas.
Even renewable raw materials are not infinitely available. The aim of a “circular bioeconomy” is therefore to re-use products as extensively as possible through closed-loop management and recycling following their utilization. In order to achieve this, recyclability must be taken into account as early as the product-development stage.
Can solid construction also be lightweight and bio-based?
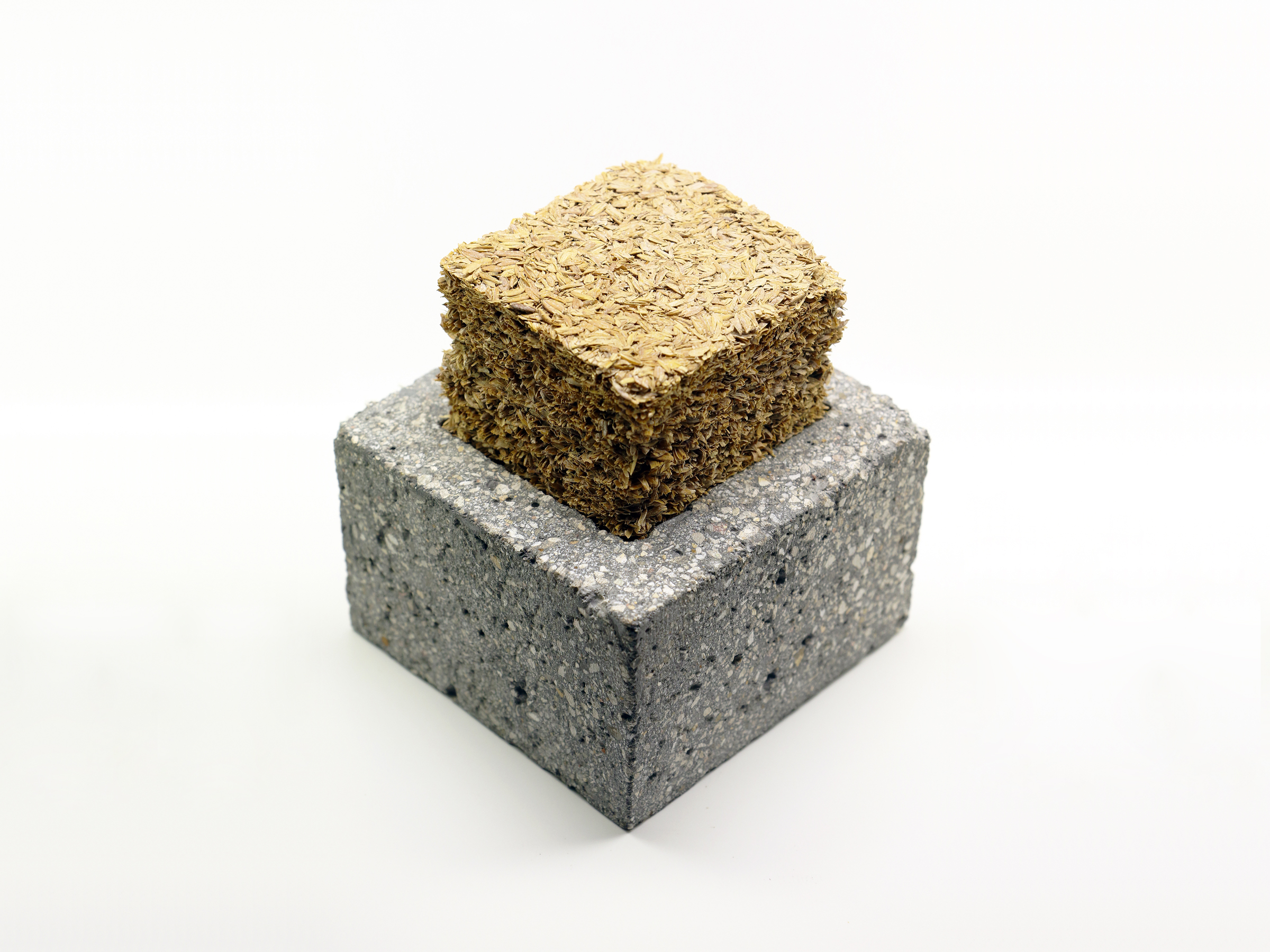
The global construction industry devours enormous quantities of fresh raw materials, in particular in the production of concrete. Furthermore, cement production causes eight percent of global carbon dioxide emissions - more than all air traffic together. Resource-conserving and climate-friendly lightweight timber constructions are gaining in popularity. Solid construction is, however, also in demand for some buildings.
Researchers at the Fraunhofer WKI have been working with partners in Germany and China on the question as to how lightweight and sustainable solid-construction products can be manufactured from construction and demolition waste as well as residual materials from forestry and agriculture. Rice is the most widely consumed food in the world. Until now, the husks have hardly been used. By means of a specific combustion process, rice-husk ash is produced, which also provides a large amount of energy. If utilized correctly, it is suitable as a cement substitute.
Gravel is used almost exclusively as a concrete aggregate. Gravel is a finite raw material whose extraction is harmful to the environment and which often has to be transported long distances to the concrete plant. Building rubble and waste wood are produced in large quantities everywhere. Until now, they have seldom – if at all – been recycled for construction purposes.
The demand for insulation materials is also huge. Insulation materials made from petroleum-based plastics, mineral wool or glass wool still dominate. Wood-fiber insulation materials are gaining in popularity, but even wood is not available in unlimited quantities. The utilization of plant residues such as straw and sawdust makes natural insulation materials more resource-efficient.
Conventional concrete and the building components made from it are heavy. Through the incorporation of plant-based aggregates and reinforcing fabrics, as well as hybrid component construction, a great deal of weight – and consequently transport energy – can be saved.
The research team uses all of these raw-material sources in the production of sustainable solid-construction products:
- Bio-recycled concrete with natural-fiber-reinforcement (instead of steel reinforcement)
- Wood shavings and straw insulation boards
- Wall system comprised of prefabricated recycled concrete blocks filled with natural insulation material for single-leaf, load-bearing walls
- Composite system made from recycled organic concrete and wood-based panels for floor slabs
This results in practicable solutions for significantly increasing the recycling rate and the utilization of renewable raw materials in the construction industry.
Are crash barriers made from wood an alternative to steel?
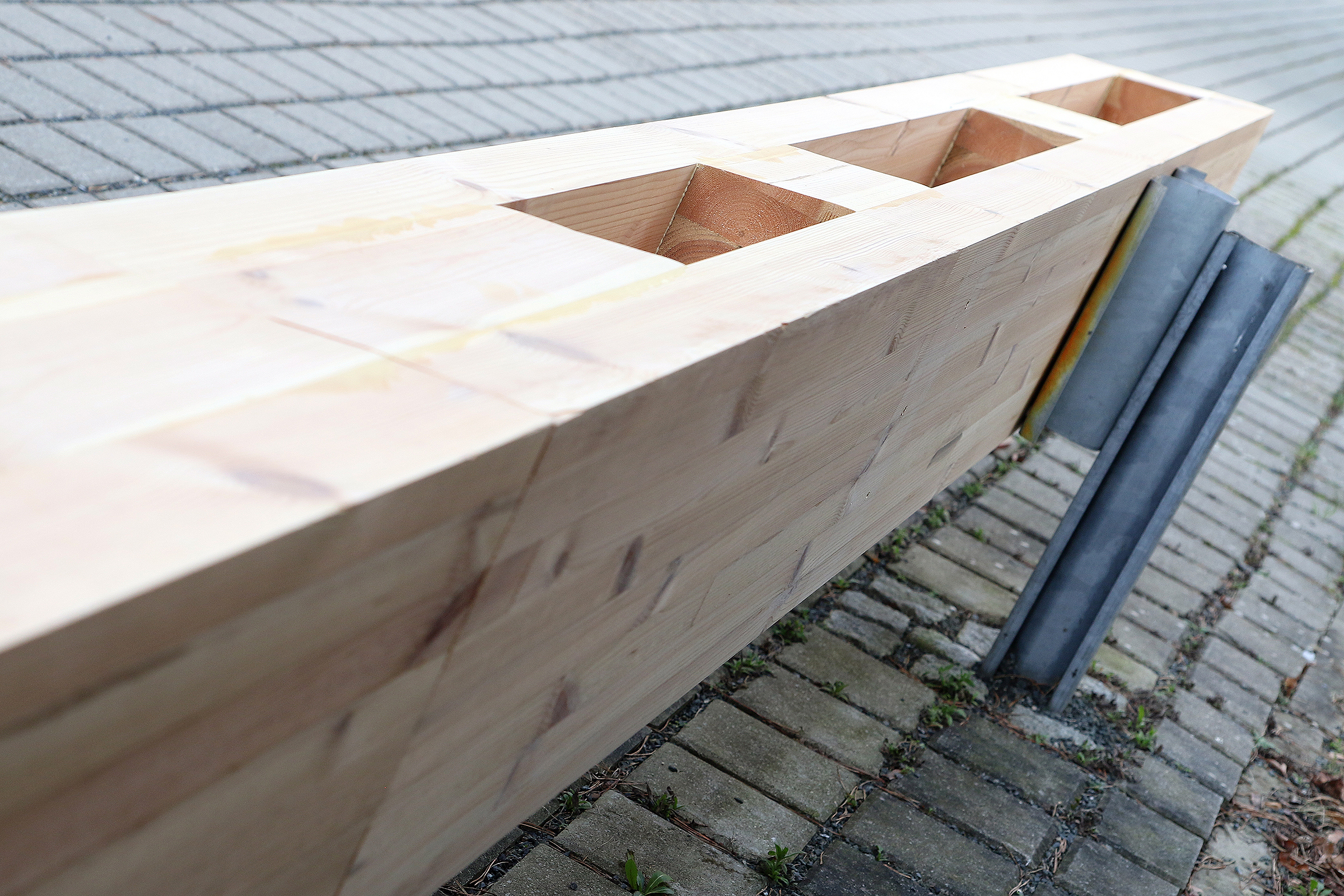
Crash barriers provide a crucial contribution towards safety in road traffic. In Germany, these are predominantly comprised of steel or reinforced concrete. In collaboration with project partners, researchers at the WKI are developing a sustainable alternative: a crash-barrier system made from indigenous wood species. It needs to be compatible with existing systems, just as durable and financially competitive.
In an earlier research project at the Technische Universität Braunschweig, a crash-barrier system made from glass-fiber-reinforced wood was developed which is compatible with existing systems made from steel. Here, the focus was on the fundamental feasibility, which was successfully verified with the aid of a demonstrator. The current project, in which the Fraunhofer WKI is participating, is the next step on the way to series production. It is to conclude with a prototype that fulfills all the substantiation required for utilization. The combination of unprotected weathering, durability and high mechanical and dynamic stresses is extremely demanding.
The crash-barrier systems used in Germany are made from bolted steel sections or prefabricated reinforced-concrete elements. The service life is assumed to be 25 years. This means that many kilometers of crash barriers are renewed every year. The production of crash barriers made from steel or reinforced concrete requires a large amount of energy and releases considerable quantities of carbon dioxide (CO2).
The deployment of wooden crash-barrier systems is an efficient means of improving the eco-balance of the construction sector. They can be manufactured using comparatively little energy and store CO2 for a long period of time.
Last modified: