Hannover Messe: Fraunhofer WKI presents lightweight products made from wood and hybrid materials
The Fraunhofer WKI will be presenting solutions for lightweight construction using renewable raw materials at the Hannover Messe from the 22nd to the 26th of April 2024. A wood-fiber-based molded part demonstrates the potential of lightweight hybrid materials and was produced using an automated molding machine. The process offers possibilities for the precision-fit production of complexly shaped components, furniture or insulation materials. Furthermore, the performance capabilities of renewable raw materials will be demonstrated with a ceiling system module on the basis of wood foam. The module can be utilized for the renovation of suspended ceilings in old buildings. The mosaic-like coffered ceilings exhibit a load-bearing capacity comparable to reinforced concrete, but are significantly lighter. The innovations can be seen on the Fraunhofer stand (Hall 2, Stand B24).
Lightweight construction is regarded as the key technology of the future. The aim of the design philosophy is to reduce weight and increase resource efficiency. A further factor is that until now, lightweight-construction applications with high mechanical requirements have been predominantly based on petrochemical products, such as fiber-reinforced polyurethane foams.
Complex components made from wood and bioplastics from the molding machine - Can that work?
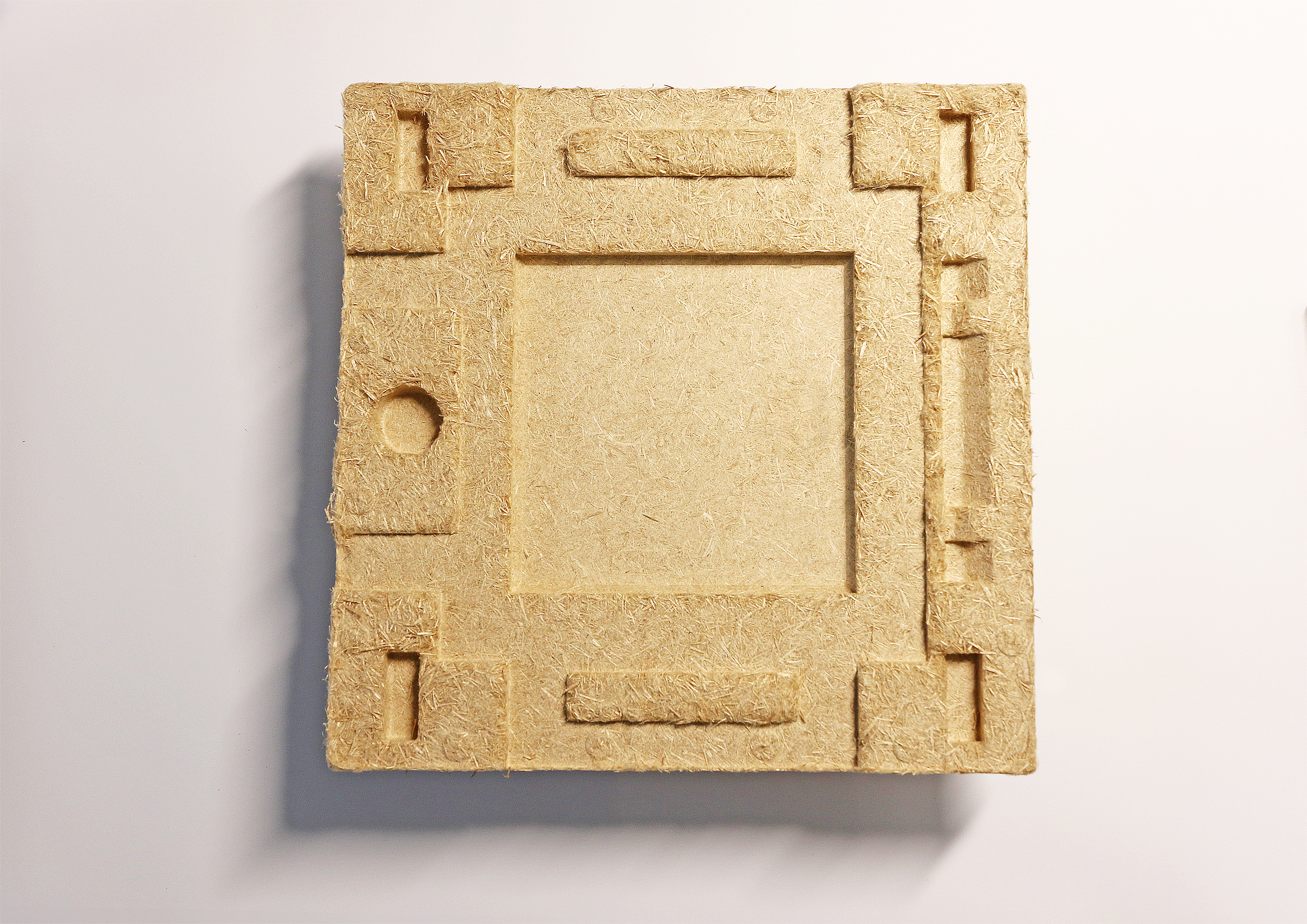
Hybrid lightweight-construction materials made from renewable raw resources are increasingly gaining importance on the market. With such materials, resource- and climate-friendly products can be manufactured that fulfill several functions - for example, load-bearing building products with integrated thermal and sound insulation as well as durable (upholstered) furniture and packaging. Efficient component geometries enable substantial weight savings with simultaneous high mechanical stability.
In collaboration with research and industry partners, researchers at the Fraunhofer WKI are developing a process for the manufacture of complexly shaped products made from wood or agricultural materials and bioplastics by means of automated molding machines. One important component of the material and technology development is furthermore the highest possible material recyclability of the products after the end of the first period of use.
Wood is a good lightweight-construction material. By nature, it has a low bulk density and high stability. Compared to modern lightweight-construction materials such as fiber-reinforced PU foams or plastics (CFRP/GFRP), wood-based materials are, however, often still relatively heavy when the mechanical requirements are fulfilled. Or they are light and possess good heat-insulating properties, but are mechanically less resilient.
The researchers at the Fraunhofer WKI are therefore combining wood particles such as fibers or chips with – preferably bio-based – polymer fibers or particle foams and processing these mixtures into extremely light and stable components using automated molding machines. The polymer content is thereby kept as low as possible, with a target of 2 percent to 7 percent.
Replacement of barely soundproofed and poorly load-bearing suspended ceilings in old buildings without reinforced concrete: Does a simple and sustainable solution exist?
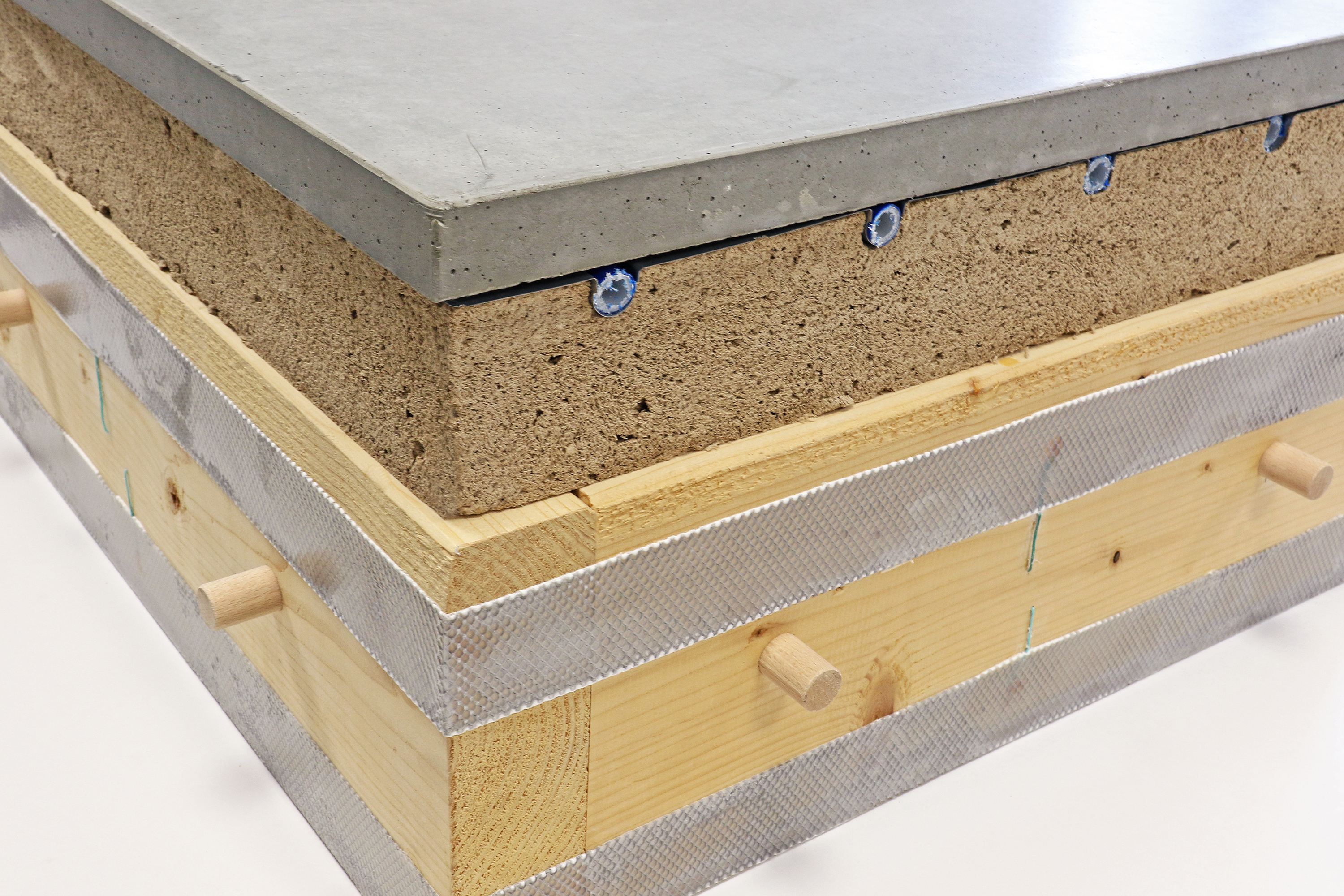
The ceiling system module consists of a high proportion of renewable raw materials and is intended to replace poorly load-bearing and barely soundproofed suspended ceilings in old buildings in the future. The area of application is extensive: Of the approximately 9 million old buildings in Germany, around 70 percent have not yet been renovated for energy efficiency. The ceiling system module was developed by researchers from the Fraunhofer WKI and the Institute of Joining and Welding (IFS) at the Technische Universität Braunschweig.
The outer box of the module consists of solid structural timber with a ceiling and a floor each made from OSB boards. The box is filled with wood foam, which was developed previously at the Fraunhofer WKI. It is not only particularly light, but also simultaneously increases thermal and sound insulation. The individual, prefabricated modules are assembled on site to form a mosaic-like coffered ceiling with a load-bearing capacity comparable to reinforced concrete. Various cover layers are possible - for example OSB board, particle board or light, thin textile-reinforced concrete. Furthermore, underfloor heating can be integrated.
The overall construction is lighter than a comparable (steel) concrete ceiling. This saves transportation energy and the associated greenhouse-gas emissions. In order to increase resource efficiency, mainly hardwoods – such as weak beech wood from thinnings – were used in the development of the modules.
With their low weight and compact size, the modules can be transported through a stairwell by two people. This is a major advantage for the renovation of old buildings that are often difficult to access.
Last modified: