Science meets design: Sustainable and aesthetic furniture made from “organic sheet material“
In collaboration with designer Jonathan Radetz, researchers at the Fraunhofer WKI have developed a lightweight item of seating furniture whose seat shell and upholstery are produced in one single step from a material known as organic sheet. The project team investigated whether used textiles can be utilized in order to manufacture an item of seating furniture in accordance with both aesthetic and sustainable criteria. The manufacturing principle can be transferred to other areas of application, such as the interior outfitting of cars.
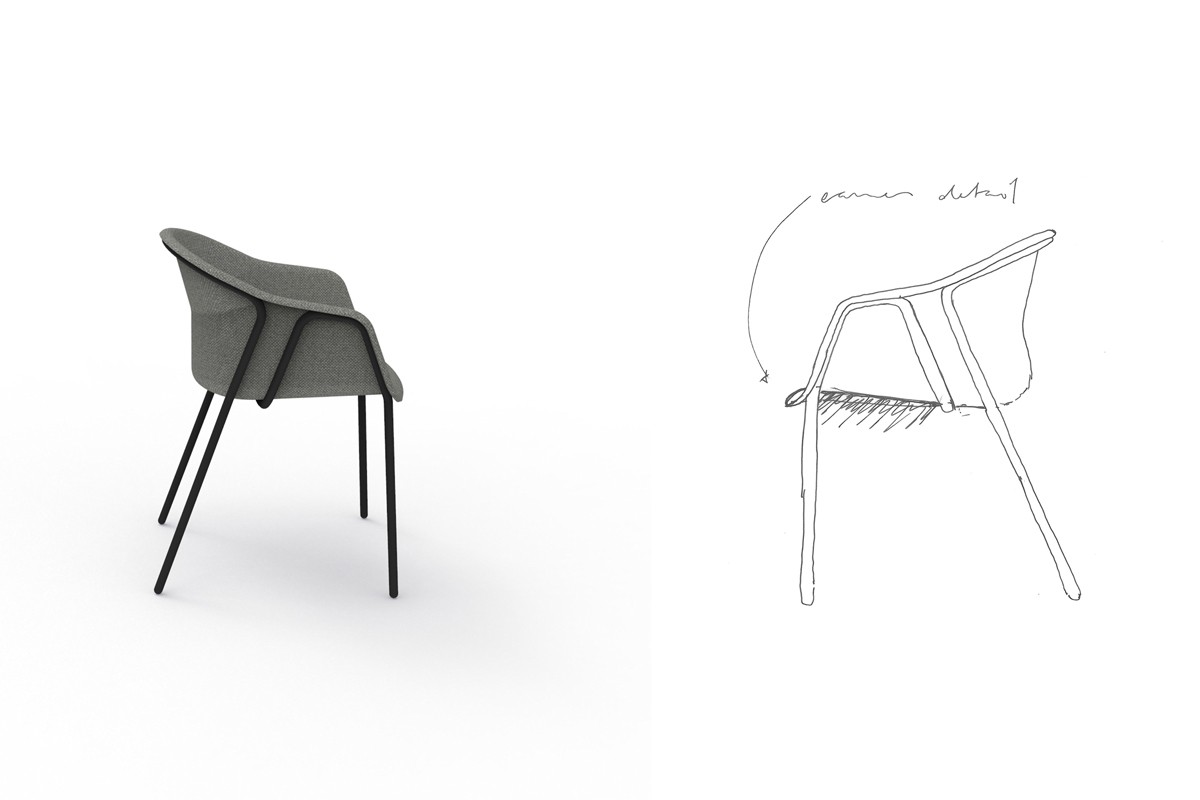
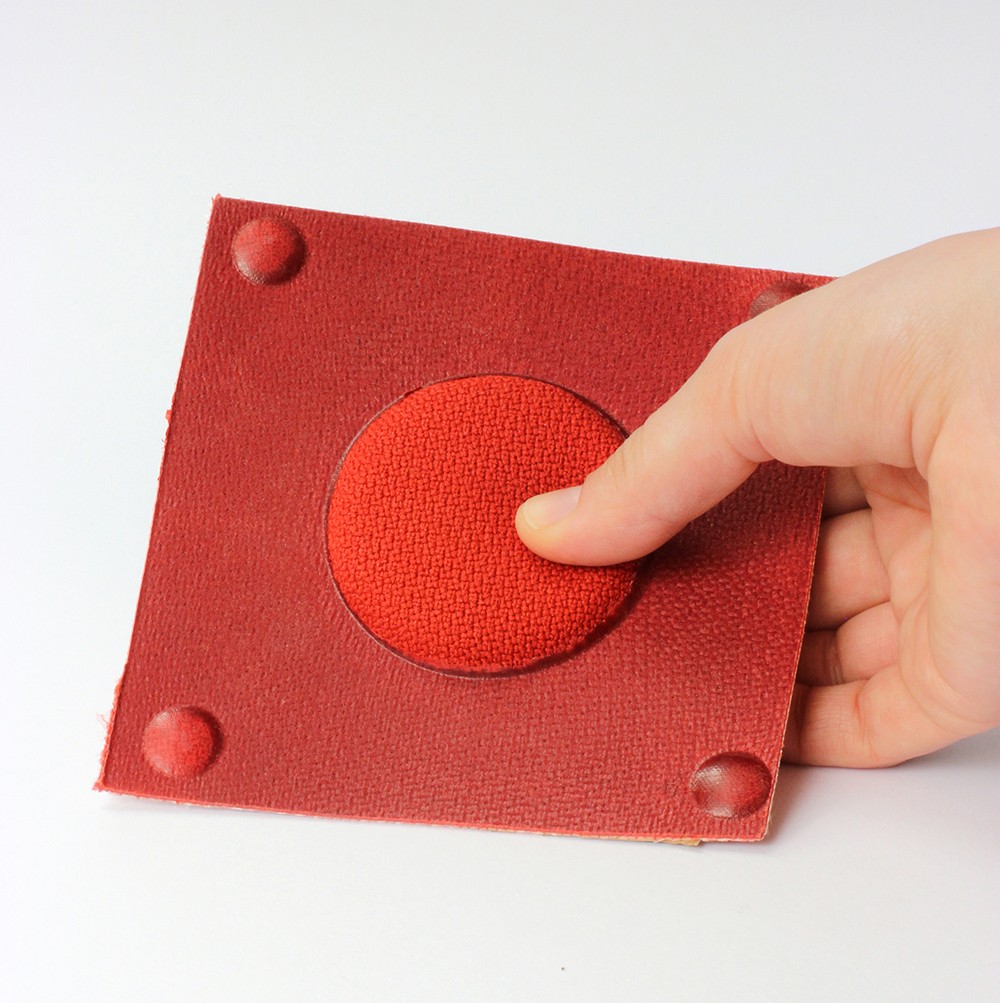
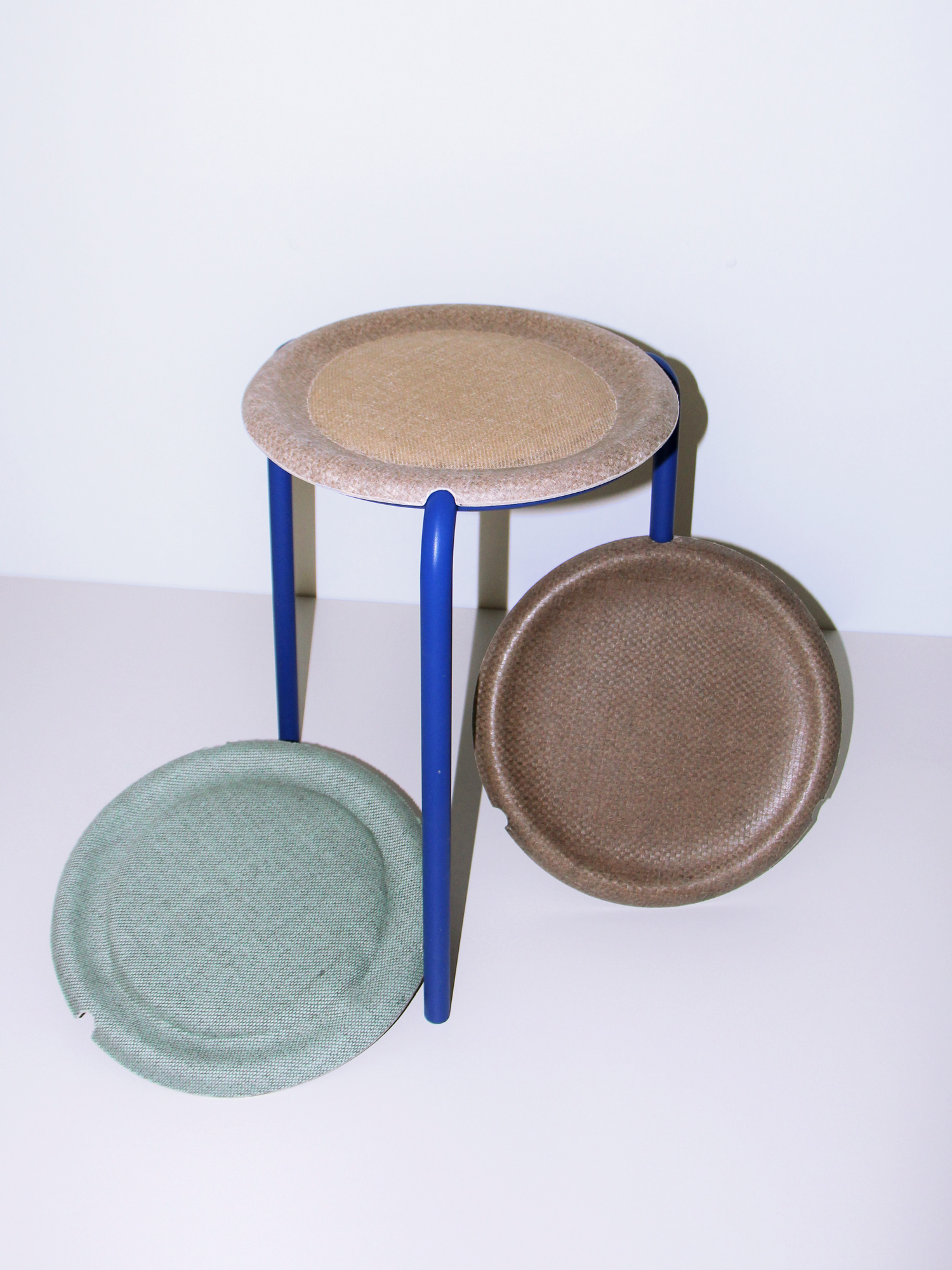
Organic sheet is a textile-based composite plastic which, due to its low weight, is particularly suitable for sustainable lightweight-construction applications. Analogous to metal sheet, organic sheet is available in continuous rolls and can be formed under the application of heat. It consists of a woven-fiber fabric that is fully embedded and consolidated in a thermoplastic matrix. The project partners were, however, unable to use conventional organic sheet for their project, as the seating area was required to have a purely textile, upholstered surface for reasons of seating comfort and haptic quality. Consequently, organic sheets featuring partial areas without a matrix were produced using discarded textiles and a plastic matrix made from polypropylene (PP), which were then molded to form a seat.
“Designer Jonathan Radetz’s idea was to embed used textiles – as woven-fiber fabrics – in a plastic matrix. Partially impregnated and consolidated fiber-reinforced thermoplastics – referred to here simply as organic sheet – enable us to implement different functions in one process step: structurally consolidated and haptic, non-structural areas. We have exploited the advantageous properties of organic sheet as a material basis in order to develop a lightweight, functional and beautifully shaped item of seating furniture,” explained Ole Hansen, Project Manager at the Fraunhofer WKI.
Jonathan Radetz, the idea-provider for the design and the material selection, exemplified the process: “Plastic matrix and fabric together serve as a load-bearing structure and support each other mutually. The fabric is embedded in the matrix and thereby simultaneously receives a protective impregnation. In the area of the seat, the impregnation is omitted and the fabric is back-filled, thereby creating padding for the seat, which we then mold to form a seat shell in the next step.”
The utilization of discarded and recycled textiles presented the project team with a particular challenge. “The exact composition of a textile is often unknown. As a result, it is difficult to predict whether the fiber and matrix will function together. Organic sheets themselves offer diverse advantages for the furniture industry. The utilization of recycled textiles has, however, proved to be complicated as the material flow for textiles is complex and difficult to reproduce. Renewable fibers such as flax have turned out to be a viable alternative for us. In a subsequent project, we would therefore like to further explore the possibilities offered by flax fibers for utilization in organic sheets,” said Mr. Hansen.
In the first phase of the project, it was determined that the use of organic sheet as a lightweight-construction material results in weight savings. This is a positive side effect, because the lighter a product is, the less energy is required for transport. In the new project phase, this advantage is to be expanded, as is the recyclability of the new products to be developed.
“In the next project phase, we would once again like to make targeted use of the creative exchange between science and design, in order to specifically further improve the closed-loop capability of our applications, which, of course, is dependent on the utilized material. In the future, by using flax fibers in a thermoplastic matrix, we would like to utilize materials that can be better re-used and consequently recycled, depending on the material composition,” said Mr. Radetz.
The partners initially selected an item of seating as a design example due to the fact that as a frequently used piece of furniture, it can illustrate the performance capability and design versatility of organic sheet with partial upholstery. “The combination of materials developed for this application example could be used in many other areas. The design approach involving the interaction of design and science and using the example of an item of seating furniture is therefore to be methodically further developed in the new phase of the project and conceptualized for other areas of application. The manufacturing process enables a high degree of diversity not only in material selection and shaping but also in prototyping and scalability. This is where we would like to continue our research, whether for use in the furniture industry or in the automotive industry,” said Mr. Hansen.
Last modified: