Bonding on demand: Switchable adhesives for cement-bonded wood-based panels
Switchable adhesives are suitable for the adhesion of cement-bonded wood-based panels. This has been verified by researchers at the Fraunhofer WKI in collaboration with industrial partners. With the aid of – amongst other things – block shear tests, the project team showed that the minimum requirements are fulfilled through the use of the newly developed adhesives.
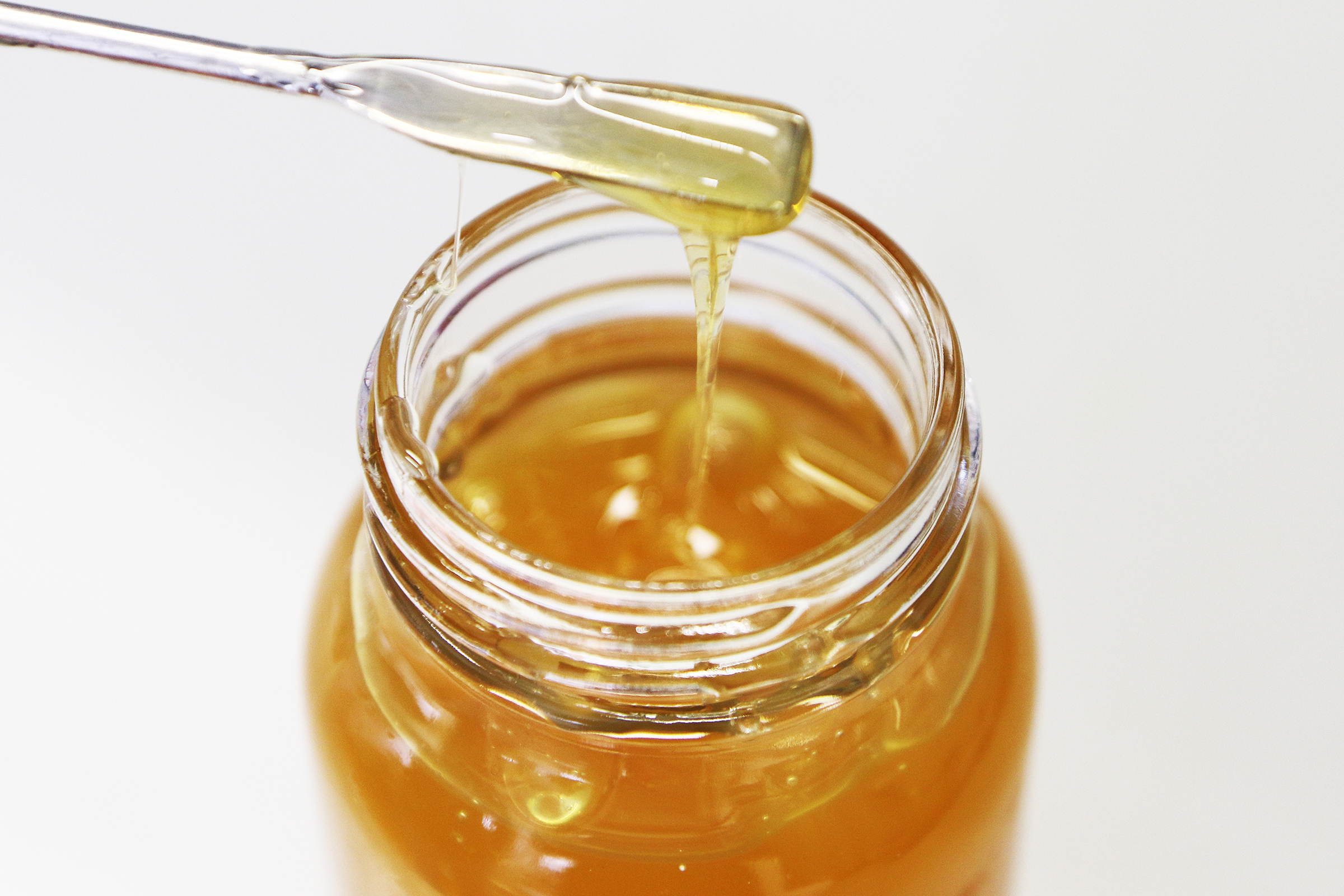
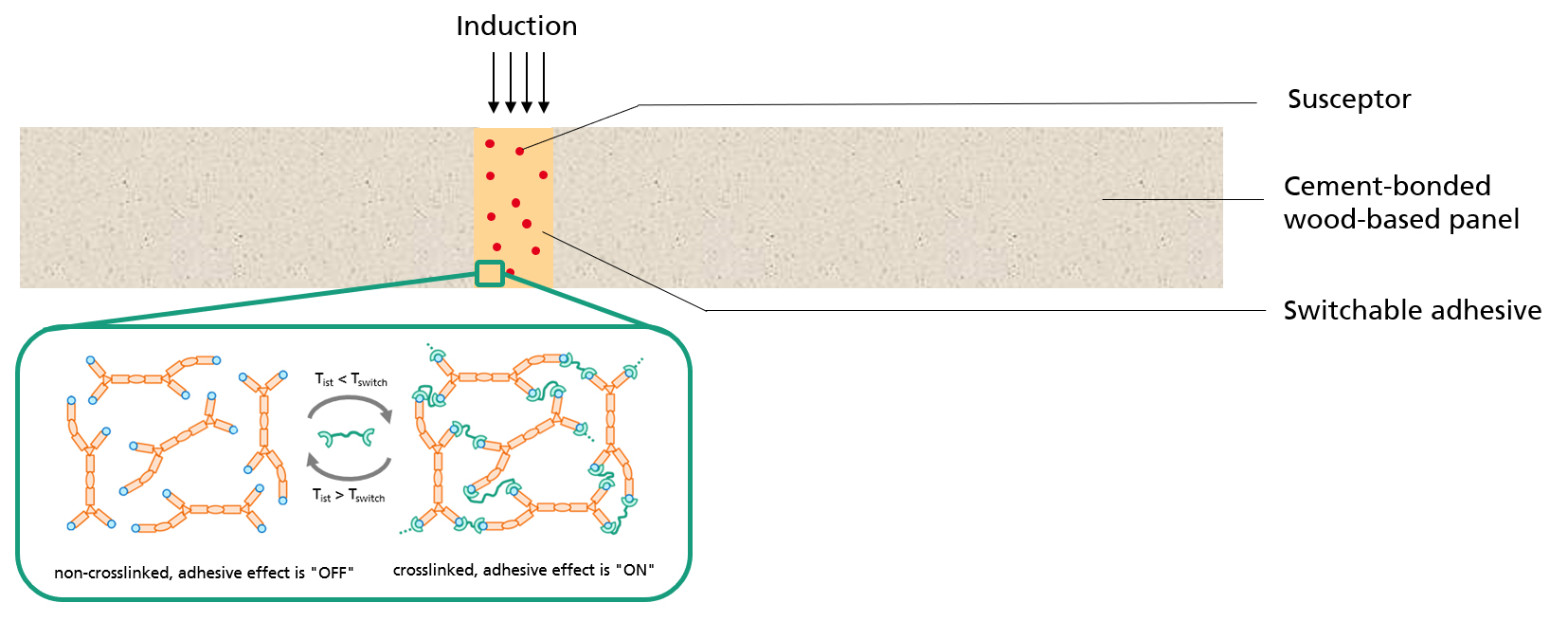
With the newly developed switchable adhesives for the face-joining of cement-bonded wood-based panels, low-offcut continuous panels can be produced within a short processing time. With the help of the industry partners, the development was tested in the laboratory under realistic conditions.
“At the Fraunhofer WKI, we have developed a bonding-on-demand adhesive whose adhesive effect can be switched on and off repeatedly. The switching of the adhesive is temperature-controlled and based on a reversible crosslinking mechanism. For this purpose, special chemical structures, so-called furan and maleimide groups, were chemically incorporated into the adhesive matrix. Below 80 °C, these units react with one another, thereby forming chemical bonds. The adhesive resin crosslinks and the adhesive effect is switched on. Above 120 °C, these bonds separate again. The crosslinking is suspended and the adhesive effect is switched off,” explained Dr. Steven Eschig, Project Manager at the Fraunhofer WKI. The researchers investigated the reversibility of the crosslinking by means of dynamic scanning calorimetry (DSC).
The researchers developed furfurylated polyurethane resins which were mixed with a bismaleimide. These were applied to cement-bonded wood-based panels and then hot-joined. Once the component had cured, the block shear strengths were tested in accordance with DIN EN 14080 Annex D. The results showed that whilst the minimum requirements of 6 N/mm2 were fulfilled, this was, however, heavily dependent on the composition of the resins.
The laboratory tests furthermore showed that the adhesive joints at the breaking point were, in places, heavily coated with cement dust, which could have had a negative influence on the bonding effect. In order to improve the bonding, the cement-bonded wood-based panels were therefore pre-treated with a primer.
The switching of the adhesive takes place via inductive excitation. For this purpose, so-called ferromagnetic susceptors were added to the adhesive resin. Through the application of an electromagnetic alternating field, the particles can be heated within seconds and the heat is transferred to the surrounding adhesive. The operating principle is comparable to an induction stove. Various susceptors, such as iron powder, stainless-steel powder, ground steel wool and MagSilica® were investigated. Ground steel wool and MagSilica® proved to be particularly suitable.
The heating behavior was analyzed by means of a thermographic examination. This showed that around 10 % weight by weight of susceptors are required in the adhesive resin in order to heat it uniformly to the required switching temperature of 120 °C. In further experiments, the influence of the strength of the electromagnetic field on the heating was investigated. For this purpose, the current strength and frequency were varied, and a thermographic camera was employed in order to determine how quickly the specimens heated up to 120 °C. At a current of 30 amperes and a frequency of 530 kilohertz, the adhesive with 10 % weight by weight MagSilica® was heated to 120 °C within 14 seconds.
This new joining technique provides increased flexibility for the utilization of cement-bonded wood-based panels in construction. “A major advantage of our adhesives is that the application and joining can be carried out independently of one another in terms of time. In comparison, commonly used adhesives have so-called pot lives, which means they can only be used for joining within a short period of time. Furthermore, the components can be separated from one another again. The components could be used for prefabricated houses that can be erected quickly and subsequently dismantled, modified and recycled,” explained Dr. Eschig.
The construction industry, which consumes large quantities of energy and raw materials, is therefore provided with a possibility for building in a more sustainable and, at the same time, more cost-efficient way.
Last modified: