Fraunhofer WKI develops sustainable multicopter with industry partners
In collaboration with the companies Leichtwerk AG and Jowat SE, the Fraunhofer WKI has developed a sustainable multicopter. Thanks to an efficient, bio-based structural design and modular construction, the new aerial vehicle is significantly more sustainable than comparable conventional systems. In order to achieve this, the Fraunhofer WKI has developed functional materials, manufacturing processes for molded parts, and suitable coatings.
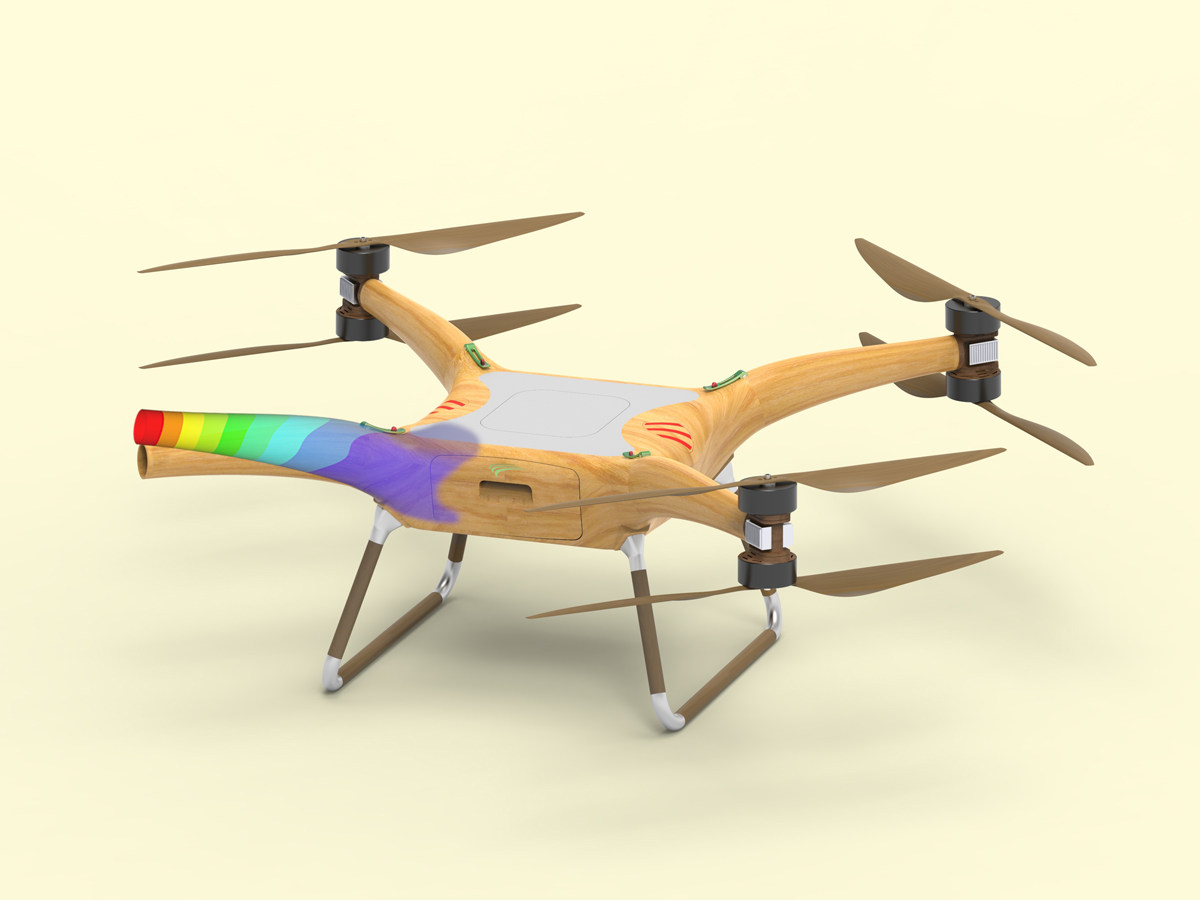
The multicopter system, made from renewable raw materials, has a take-off mass of 25 kilograms and a large payload area. As a result of its modular design, it can be adapted for specific application cases. The drone system is designed to be waterproof and dustproof.
The civilian market for drones has been growing for several years, and in particular multicopters are in high demand. The market growth has led to a high consumption of critical materials for multicopter production. “Our goal was therefore to develop a resource-efficient multicopter system on the basis of renewable, regionally available raw materials. Multicopters currently available on the market are generally made from fiber-reinforced plastics. The new multicopter system should primarily utilize raw materials that are produced in Germany,” said Dr. Arne Schirp, Project Manager at the Fraunhofer WKI.
The overall concept for the multicopter system originates from Leichtwerk AG, who coordinated the joint project and undertook the aeronautical development. For testing and optimization, extensive operational and flight tests were carried out. The project partner Jowat SE was entrusted with the development of suitable adhesive systems. The Braunschweig-based company Auro provided coating systems on the basis of renewable raw materials, which were tested for application in the drone.
“Up to now, conventional, fiber-reinforced plastics have been used for virtually all multicopters available on the market. They usually consist of fibers (carbon, glass or aramid) and petrochemical polymers. Their high specific strengths and rigidities surpass, to some extent, the load requirements of multicopters. Our goal at the Fraunhofer WKI was to develop and manufacture materials that fit precisely, are more sustainable, adequately fulfill the load requirements, and are predominantly made from renewable resources. It was also important to ensure that any defective components could be easily replaced,” explained Dr. Schirp.
The following material classes are utilized for the new multicopter: laminated materials made from 3D veneers, natural-fiber-reinforced thermosetting plastics, and thermoplastically processable, natural-fiber-reinforced bioplastics.
By testing various approaches, it was possible to successfully develop the processes in order to create veneer-based components with the desired form. The researchers were also able to develop processes for producing components from flax-fiber prepreg and flax fabric.
For the optimization of the materials, the researchers conducted diverse tests, amongst others with regard to rigidity, strength, water absorption and swelling. The coatings were tested by means of, for example, artificial and natural weathering cycles. The developed materials were utilized in prototype development.
The airworthiness of the prototype was verified in a test flight. A film and further information can be found here: https://www.linkedin.com/feed/update/urn:li:activity:7086656105862291456/
Last modified: