Lignin foam:
Sustainable bio-foam made from lignosulfonate for car bumpers and further applications
The wood constituent lignin accrues in large quantities as a by-product of pulp and paper production. In collaboration with industrial partners, we are developing a high-performance bio-foam from lignin. In order to demonstrate its market potential, the lignin foam is being processed into molded parts for the automotive industry within the scope of the project. These parts are to be utilized as the core in car bumpers. Petrochemical foam materials could also be replaced by climate-friendly lignin foams in numerous other applications - for example in packaging, insulation materials or as a core material in wind-turbine rotor blades.
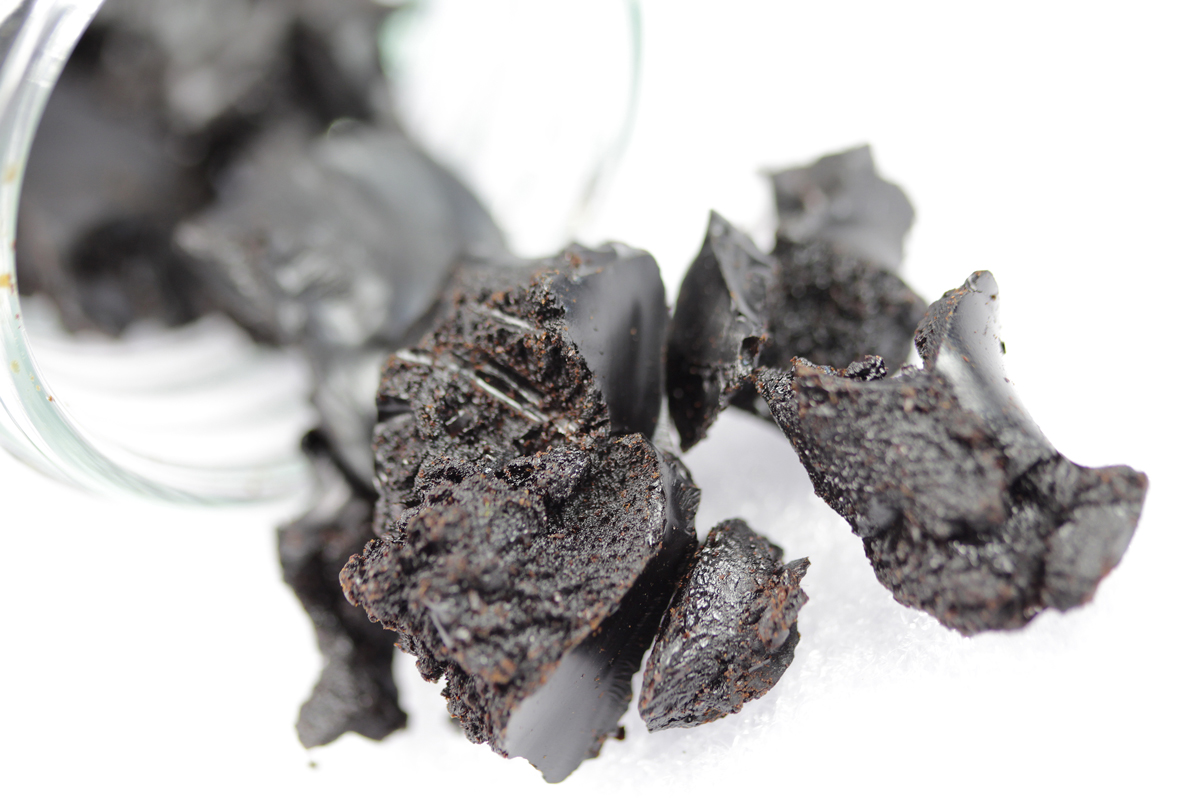
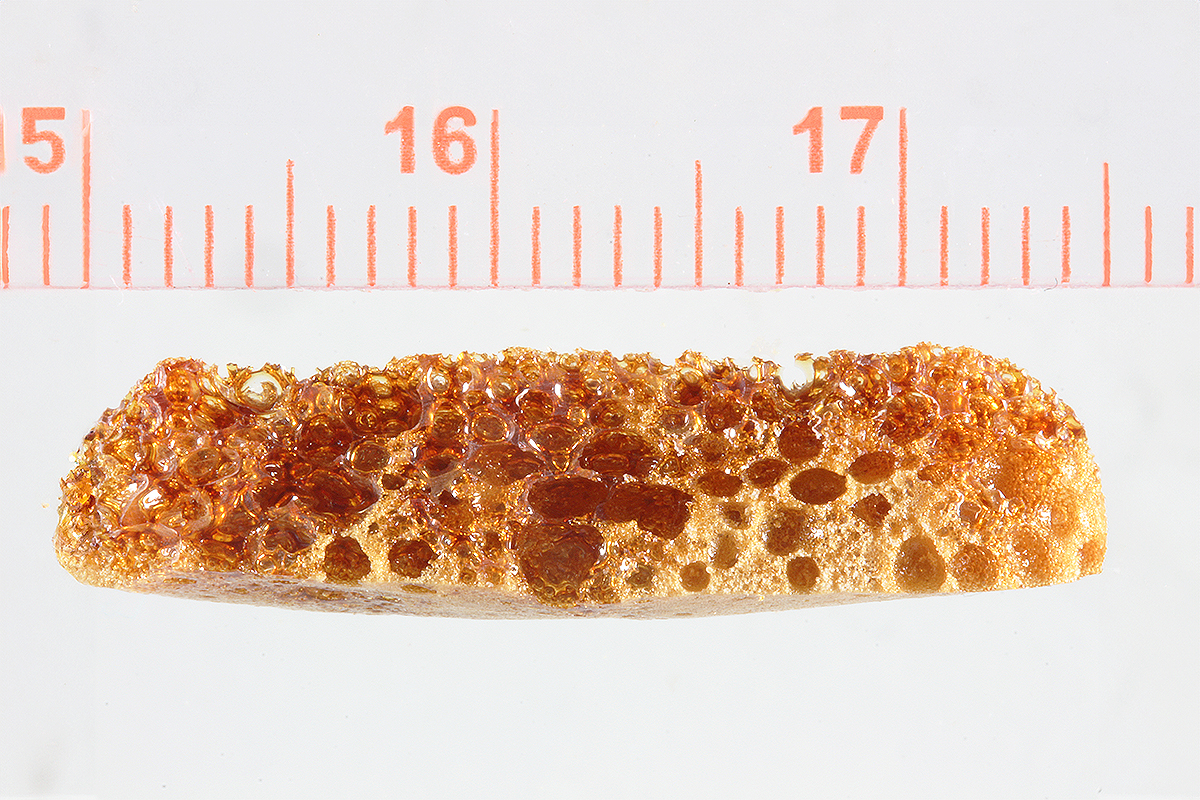
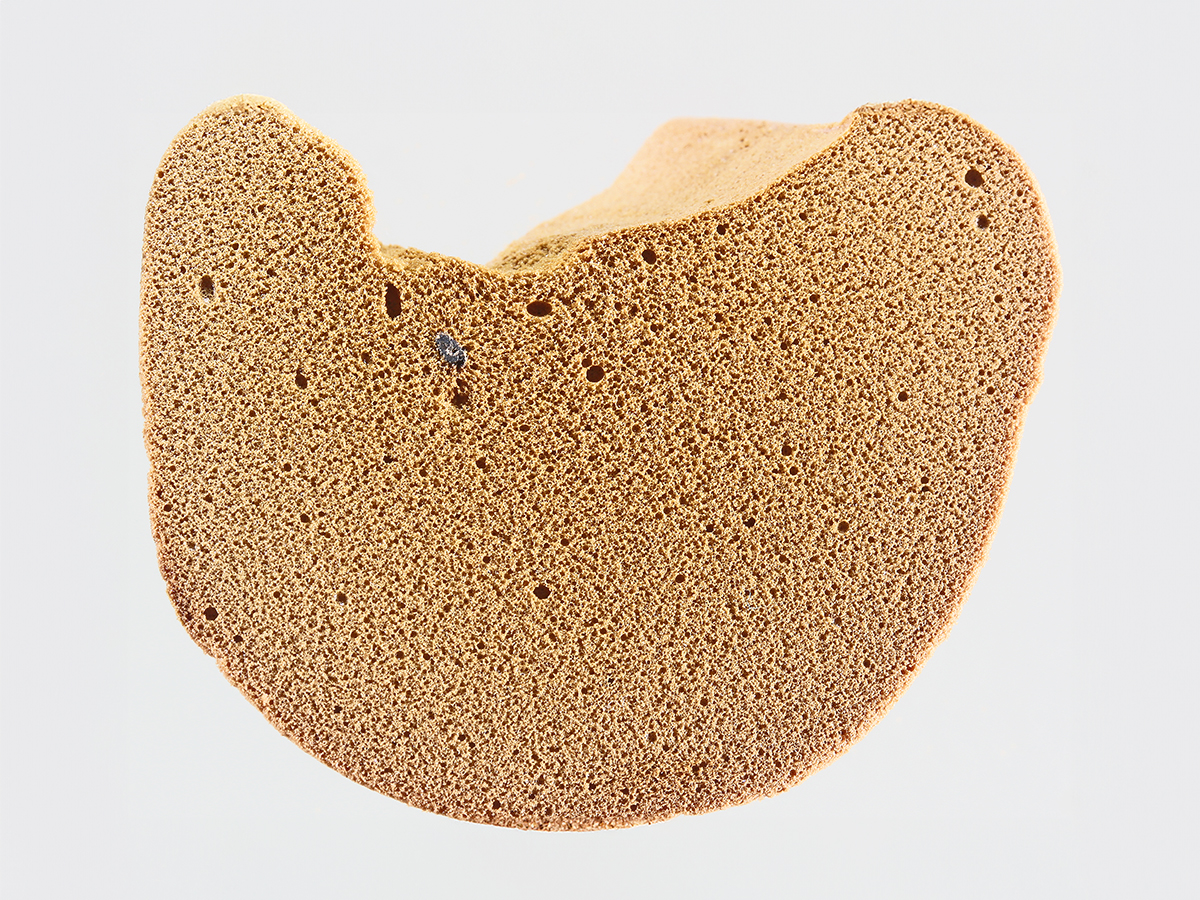
The chemical pulping of plant fibers produces pulp, which consists primarily of cellulose and which is an essential raw material in paper production. Depending on the pulping process, kraft lignin, soda lignin or lignosulfonates accrue as by-products. In Germany, the magnesium bisulfite process is widely used due to its low odor nuisance. The lignin sulfonates produced in this process were therefore selected as the raw-material source for this research project.
Previously developed “lignin foams” are polyurethane foams that contain a maximum of 40 percent lignin. Our aim is to develop a solely lignin-based foam. In order to be economically competitive with petrochemical foams, cost-intensive purification of the lignin should furthermore be avoided. To this end, we are developing a process for foaming and cross-linking non-purified lignin sulfonates in which the reaction is not adversely influenced by impurities. On the contrary: Other residual materials from the plant-pulping process, such as non-digested fiber bundles and rejects, are to be specifically used to strengthen the foam.
Through the foaming process and targeted reinforcement, a suitable compressive elasticity should be achieved. It is necessary for the foam to possess a certain degree of elasticity if it is to be utilized in car bumpers, as this reduces the risk of injury for pedestrians and cyclists.
In order to achieve a 100 percent biogenic foam, we are also investigating which bio-based additives are suitable as foaming reagents.
Based on the results of the foam development, the industrial partners will subsequently undertake the construction of a molded-part production plant, the designing of the bumpers, and the production and testing of bumpers with a lignin-foam core as technology demonstrators.
Last modified: